Цифровые двойники помогут России повысить производительность труда
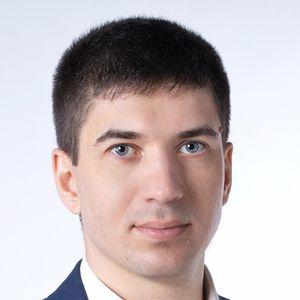
Воронин
руководитель направления бизнес-аналитики компании BIA-Technologies
Одной из болезней российской промышленности часто называют низкую производительность труда. Однако корень проблемы не столько в качестве кадров, сколько в низком уровне цифровизации. Какие меры необходимо принять, чтобы сократить отставание от ведущих экономик в области автоматизации, роботизации и интеллектуальных систем, рассказывает руководитель направления бизнес-аналитики компании BIA-Technologies Станислав Воронин.
По уровню производительности труда (отношение ВВП к рабочему времени) Россия в рейтинге Организации экономического сотрудничества и развития (ОЭСР) находится на 36 месте из 45 возможных с показателем в 31,2 долларов. У США он составляет 87 долларов, у Германии – 75 долларов. При этом медленный темп роста показателя России не дает догнать другие страны, даже не смотря на то, что мы относимся к числу самых многоработающих стран.
Одна из причин, низкой производительности в России – отставание от ведущих экономик в области автоматизации, роботизации и интеллектуальных систем. Так, значение индекса цифровизации промышленности для России, рассчитанное НИУ ВШЭ, составляет 36 из 100 возможных. Россия находится в соответствующем рейтинге стран на 21-ом месте из 27. В этих условиях цифровые двойники могут стать эффективным инструментом модернизации промышленности и улучшения базовых показателей множества отраслей.
Что такое цифровые двойники
Цифровой двойник – интеллектуальная копия реального физического процесса или объекта. Модели создаются для оборудования и устройств, производственных процессов, всего предприятия или отрасли. Цифровой двойник существует в виде 2D- или 3D-моделей, которые работают с различными сценариями технологических процессов.
Одно из главных достоинств технологии – это возможность проводить эксперименты и проверять гипотезы в безрисковой среде. То есть моделировать процессы, закладывать те или иные свойства товаров, оценивать эффективность замены оборудования и перераспределять персонал, не опасаясь, что это может негативно сказаться на реальном производстве.
Более того, виртуальная среда дает возможность ускорять процессы в десятки, сотни, тысячи раз. Так, результаты изменений в производственном цикле или на складе могут стать заметны только через несколько недель и даже месяцев. Цифровой двойник позволяет оценить эффект от изменений в считанные часы, минуты. И если результаты недостаточно хороши, то отработать другую гипотезу.
По нашим наблюдениям, практика применения технологии показывает, что стоимость производственных изменений при проектировании с помощью цифровых двойников на 10% ниже, чем при использовании традиционных методов. Отработка гипотез на моделях в принципе сокращает затраты на модернизацию и оптимизацию производства. Ни уже используемые на производстве MES-системы (Manufacturing Execution System, система управления производственными процессами), ни тем более Microsoft Excel не обладают достаточными возможностями для построения сложных моделей. При этом на базе цифровых двойников могут быть запущены APS-модули (Advanced Planning & Scheduling, система синхронного планирования производства).
Как работают цифровые двойники
С помощью цифровых двойников можно решать стратегические, тактические и операционные задачи. Примером стратегической задачи может быть проектирование и строительство производственной линии, разработка программы технического перевооружения и открытие нового предприятия. Тактический уровень – это оптимизация производственной программы, внутрипроизводственной логистики или оптимальное управление запасами. Операционные задачи – прогнозирование состояния системы/объекта, функция цифрового советчика технологической операции (подбор оптимальных параметров в онлайн-режиме).
Информационный ландшафт современного предприятия уже включает в себя целый ряд систем: ERP (Enterprise Resource Planning, планирование ресурсов предприятия), PLM (Product Lifecycle Management, управление жизненным циклом продукции), WMS (Warehouse Management System, система управления складом), MDC (Machine Data Collection, система мониторинга промышленного оборудования), EAM (Enterprise Asset Management Systems, системы управления активами предприятия), MES (Manufacturing Execution System, система управления производственными процессами). Однако их недостаточно для решения задач оптимизации, которые чаще всего на производстве доверены опыту начальника цеха. Внедрение APS-модуля, базирующегося на цифровом двойнике, позволяет прогнозировать сроки выполнения заказов, планировать производство с учетом имеющейся загрузки, оптимально выстраивать график работы производственного персонала.
Например, на одном из ведущих российский кабельных предприятий производство на 95% происходит "под заказ". Раньше оптимальный план для распределительного центра можно было построить на 2-3 дня вперед, а для всего завода в целом вообще нельзя, так как не было гарантированной методики. При этом у разных подразделений завода – сбыта, производства, снабжения – разные цели. На этом фоне как-то скоординировать производственные KPI с непроизводственными было практически невозможно.
В итоге был внедрен APS-модуль, и предприятие научилось строить два плана. Большой план для завода в целом по всему горизонту заказов. Попутно рассчитываются даты для новых заказов, оптимизируются ранее назначенные работы и рассчитываются потребности в материалах. Малый план создается для завода в целом на 2-3 дня. При этом он оптимизируется только в границах, рассчитанных большим планом, при пересчете которого зону малого затрагивают минимальным образом. Вместе с тем, оба плана строятся по одному и тому же KPI. Внедрение APS-модуля на кабельном предприятии заняло полтора года, но система окупилась уже за первый месяц, так как KPI подразделений вырос на 5%.
В сухом остатке
Согласно подсчетам BIA-Technologies, внедрение цифровых двойников на 9-12% повышает эффективность использования оборудования и на 2-5% - производительность труда, на 7-9% сокращает сроки выпуска продукции и время простоя - на 8-10%. В результате, в целом затраты предприятия снижаются на 8-12%, а внедрение цифровых двойников и использование APS-модулей окупается на производстве в среднем менее чем за полгода.
Сегодня многие российские компании присматриваются к цифровым моделям предприятия, производства и отдельных процессов. Более того, Россия стала первой страной, утвердившей стандарты в области цифровых двойников: ГОСТ Р 57700.37–2021 "Компьютерные модели и моделирование. Цифровые двойники изделий. Общие положения" начнет работать с 1 января 2022 года. Таким образом, благодаря высокому уровню отечественной школы математического моделирования и активной позиции экономического руководства страны, у нас есть все шансы в этой сфере догнать и перегнать цивилизованный мир.
